Кантроль працэсаў вытворчасці вермікулярнага жалеза
У параўнанні з шэрым жалезам трываласць на расцяжэнне вермікулярнага жалеза павялічваецца прынамсі на 70%, модуль пругкасці павялічваецца на 35%, а трываласць на стомленне павялічваецца амаль удвая. У параўнанні з алюмініевым сплавам трываласць і цвёрдасць вермікулярнага жалеза ў два разы вышэй, а стомленасць - у два разы. Гэтыя характарыстыкі вермікулярнага жалеза даюць магчымасць рухавіку палепшыць суадносіны магутнасці/вагі і павялічыць ціск у цыліндры. Павышэнне ціску ў цыліндры-залог аптымальнай прадукцыйнасці дызельнага рухавіка наступнага пакалення з непасрэдным упырскам. Каб задаволіць шырокае прымяненне вермікулярнага жалеза, ліцейная прамысловасць у цяперашні час актыўна рыхтуецца, укладвае значныя сродкі і аднаўляе новыя працэсы, каб зрабіць вытворчасць вермікулярнага жалеза стабільным і надзейным.
Для рухавікоў з вермікулярнага жалеза ад прататыпа да масавага вытворчасці вырашальным фактарам з'яўляецца рызыка якасці. Для высакаякаснага вермікулярнага жалеза стабільная зона вельмі малая, толькі ў межах 0.008% утрымання магнію. Слядовая колькасць, напрыклад страта 0.001% магнію, прывядзе да ўтварэння пластовага графіту, што прывядзе да зніжэння механічных уласцівасцяў на 25-40%. У гэтым артыкуле апісана сістэма кіравання працэсамі, заснаваная на метадах тэрмічнага аналізу. Сістэма вымярае страты магнію і рэгулюе стан расплаўленага жалеза ў Інтэрнэце, каб прадухіліць адукацыю шматкі графіту. Гэты онлайн -метад кантролю вымярэнняў і рэгулявання зніжае лятучасць у працэсе вытворчасці вермікулярнага жалеза да самай нізкай кропкі і прынцыпова ліквідуе рызыку якасці, выкліканы вытворчасцю вермікулярнага жалеза.
Попыт на высокія конскія сілы, высокі крутоўны момант, нізкія выкіды выхлапных газаў і зніжэнне расходу паліва працягвае расці. Гэта прымушае канструктараў магутных дызельных рухавікоў павялічваць пікавы ціск запальвання, што значна павялічвае цеплавую нагрузку і механічную нагрузку рухавіка. Цеплавая нагрузка і механічная нагрузка павялічваюцца адначасова, так што звычайныя чыгунна -легаваныя чыгунныя рухавікі (CrMo), якія выкарыстоўваюцца ў цяперашні час, дасягнулі або перавысілі верхнюю мяжу іх выкарыстання. Вытворцам рухавікоў патрэбныя матэрыялы з больш высокай трываласцю і лепшай тэрмаўстойлівасцю.
Чырвонае жалеза хутка стала матэрыялам выбару для людзей. Гэта значна павышае надзейнасць блока цыліндраў, ГБЦ і гільзы цыліндраў новага пакалення рухавікоў грузавікоў. Для таго, каб дасягнуць найлепшага спалучэння розных уласцівасцяў (напрыклад, уласцівасцяў ліцця, апрацоўкі, цеплаправоднасці і механічных уласцівасцяў), гэтыя дэталі павінны быць выкананы з хуткасцю сфероідацыі ад 0% да 20% (хуткасць паўзучасці ад 80% да 100% ) Зроблена з вермікулярнага жалеза. Калі хуткасць сфероидизации перавышае 20%, гэта выкліча шэраг неспрыяльных фактараў. Напрыклад, колькасць ўсаджвання занадта вялікае, а дэталі са складанай формай, такія як галоўкі цыліндраў, асабліва схільныя да ўсаджвання. Іншы прыклад - скарачэнне тэрміну службы інструмента з -за празмернага зносу падчас апрацоўкі. Таксама назіраецца значнае зніжэнне цеплаправоднасці, што выклікае цеплавое напружанне і гэтак далей. На другім канцы вермікулярнага жалеза з'яўленне лускаватага графіту прывядзе да лінейнага зніжэння механічных уласцівасцей, у выніку чаго рухавік не зможа задаволіць новыя патрабаванні. Такім чынам, каб задаволіць патрэбы новага пакалення рухавікоў грузавых аўтамабіляў, хуткасць сфероідацыі высокатрывалага вермікулярнага жалеза павінна складаць ад 0% да 20% (гэта значыць хуткасць паўзучасці вышэй 80%, без шматкоў).
Выкарыстоўваць ці не кіраванне вытворчым працэсам, залежыць ад гадавога выпуску прадукту, складанасці прадукту і дапушчальнага дыяпазону змяненняў у металаграфічнай структуры. Як паказана на малюнку 1, адносна простыя дэталі з невялікім аб'ёмам, такія як формы для зліткаў, звычайна можна вырабляць звычайнымі метадамі ліцця. Кантроль працэсаў, як правіла, не патрэбны, і ён эканамічна не выгадны. Калі павялічваецца гадавы аб'ём камплектуючых, такіх як выхлапныя трубы, рукава -маніпулятары і кранштэйны, варта ўводзіць кантроль за працэсам. Нягледзячы на тое, што гэты від прадукцыі мае вялікі гадавы аб'ём вытворчасці, гадавы аб'ём ліцця не высокі. Патрабаванні да металаграфічнай структуры не вельмі жорсткія, што дазваляе частаце сфероідызацыі дасягаць 50%. Акрамя таго, з -за невялікай колькасці механічнай апрацоўкі такіх дэталяў павелічэнне тытана, якое можна дадаць у вытворчасць, можа дазволіць пашырыць кантраляваны дыяпазон. Для вытворчасці гэтага віду жалеза звычайна падыходзяць звычайныя метады ліцця і строгае навучанне. Але з пункту гледжання кантролю якасці, кантроль працэсаў павінен быць больш бяспечным. Сапраўды гэтак жа кантроль за працэсам таксама дае гарантыю на вытворчасць буйных блокаў суднавых рухавікоў і галовак цыліндраў. Нягледзячы на тое, што вялікія памеры і нізкая колькасць вытворчасці спрыяюць вытворчасці прадукцыі, эканамічных страт, выкліканых прадуктамі, якія перавышаюць стандарт, дастаткова, каб дадаць набор сістэм кіравання працэсам.
Прадукты, якія найбольш патрабуюць кантролю за працэсам, - гэта блокі цыліндраў аўтамабільных рухавікоў, галоўкі цыліндраў і тармазныя дыскі з вялікай гадавой магутнасцю, высокай складанасцю і строгімі тэхнічнымі патрабаваннямі. Гадавы аб'ём вытворчасці і гадавы танаж гэтай прадукцыі вельмі высокія. Яны складаныя па памеры, патрабавальныя да металаграфічнай структуры і маюць тэндэнцыю да ўсаджвання паражнін. Гэтыя прадукты не павінны несці ніякіх рызык якасці, інакш страта будзе вельмі сур'ёзнай.
Строгія патрабаванні да прадукцыйнасці блока рухавіка, галоўкі цыліндраў і сядзення цыліндру заклалі аснову для тэхнічных характарыстык вытворчасці. Для таго, каб атрымаць лепшыя ўсебаковыя характарыстыкі ліцця, апрацоўкі і механічных уласцівасцяў, хуткасць сфероідацыі павінна знаходзіцца ў дыяпазоне ад 0% да 20% ва ўсіх ключавых частках кампанента. Што яшчэ больш важна, трэба цалкам пазбягаць лускаватага графіту, каб прадухіліць пашкоджанне частак, выкліканае мясцовай слабасцю. Для дасягнення добрай механічнай дабаўкі свабодныя карбіды неабходна звесці да мінімуму. Таму ні ў якім разе нельга дадаваць тытан. Нарэшце, з пункту гледжання вытворчасці, ліцейны завод мае патрэбу ў стабільным і надзейным працэсе, каб забяспечыць найменшую норму лому, выкліканую металаграфічнай структурай. Вытворцы ў аўтамабільнай прамысловасці патрабуюць забеспячэння якасці, і 100% адлівак павінны адпавядаць металаграфічным патрабаванням. Маштабная і надзейная вытворчасць блокаў цыліндраў, галовак цыліндраў і сядзенняў цыліндраў патрабуе дакладнага аналізу і онлайн-налады расплаўленага жалеза, каб выключыць ваганні ў працэсе перад заліваннем.
Вермікулярная ўстойлівасць жалеза
Прычына таго, што ўшчыльненае жалеза не выкарыстоўваецца ў вялікіх колькасцях для вытворчасці складаных дэталяў (напрыклад, блокаў рухавікоў), заключаецца ў тым, што стабільная плошча ўшчыльненага жалеза занадта малая, каб гарантаваць адсутнасць рызыкі ў вытворчасці. Наогул кажучы, гэтая стабільная зона ахоплівае толькі плошчу 0.008% магнію, як паказана на малюнку 2. Памер і становішча платформы ў стабільнай зоне змяняюцца ў залежнасці ад прадукту. На самай справе, даступны дыяпазон магнію меншы за гэты. Паколькі кожныя 5 хвілін актыўны магній будзе спальваць 0.001%. Пачатковая тэмпература плаўлення расплаўленага чыгуну павінна быць дастаткова далёка ад рэзкага павароту ўшчыльненага жалеза да шэрага жалеза, каб гарантаваць, што ў апошняй адліванай частцы не з'явіцца шматкі графіту. Калі да расплаўленага жалеза дадаецца магній, прыкладна праз 15 хвілін з'явіцца шматкі графіт.
Зыходная кропка не павінна быць занадта блізка да правай частцы стабільнай платформы (высокае ўтрыманне магнію), інакш гэта прывядзе да таго, што ў тонкай частцы і ў частцы хуткага астуджэння ўтворыцца вялікая колькасць сфероіднага графіту.
У дадатак да невялікай даступнай плошчы платформы, зона платформы заўсёды рухаецца. Калі ўтрыманне актыўнага кіслароду і серы высокае, яны будуць спажываць больш актыўнага магнію, і ўся платформа перамесціцца направа (высокае ўтрыманне магнію). І наадварот, калі ўтрыманне актыўнага кіслароду і серы нізкае, платформа перамесціцца налева (нізкае ўтрыманне магнію). Змены ў складзе сыравіны, чысціні, ступені акіслення і вільготнасці і г.д. робяць немагчымым кіраванне людзьмі вермікулярнага жалеза з фіксаваным дыяпазонам хімічнага складу.
Нягледзячы на тое, што пры пераходзе з вермікулярнага жалеза ў шэрае жалеза неабходна толькі знізіць актыўны магній на 0.001%, спальванне магнію не прыводзіць да таго, што ўся частка ператворыцца ў шматкі графіт. Калі актыўнага магнію недастаткова, графіт спачатку ўтварае шматкі і пашыраецца вонкі пры застыванні, а магній прасядае і канцэнтруецца на пярэднім канцы раздзелу цвёрдая вадкасць. Калі пачатковая колькасць актыўнага магнію падыходзіць, вермікулярны графіт будзе ўтварацца на мяжы эўтэктыкі, як паказана на малюнку 3. Графіт шматкоў спачатку з'яўляецца ў выглядзе рассеяных шматкоў графітавых плям. У адрозненне ад усіх звычайных графітавых шматкоў, гэтыя ізаляваныя графітавыя плямы лускавінак цяжка выявіць з дапамогай ультрагуку. Верагоднасць іх сканавання ультрагукам не высокая.
Адчувальнасць магнію да вермікулярнага жалеза можа быць паказана на малюнку 4: У тону гарачага металічнага коўшыка, проста дадайце 10 грам магнію, плямістыя графітавыя плямы, рассеяныя ў доследным узоры Φ25, могуць цалкам ператварыцца ў вермікулярны графіт. Межа трываласці на выпрабаванне з дошчачкі графітавых плям складае ўсяго 300 МПа, у той час як трываласць на разрыў той жа пробы з поўным уцячэннем дасягае 450 МПа.
Інакулянт таксама вельмі адчувальны да стабільнай платформы вермікулярнага жалеза, як паказана на малюнку 5: даданне 80 грам прышчэпкі да адной тоны расплаўленага жалеза павялічыць хуткасць сфероідацыі ў тэставым бары Φ25 з 3% да 21%. Колькасць прышчэпкі вялікая, а ядро крышталя вялікае, што спрыяе адукацыі сферычнага графіту. Гэта падымае вермікулярную жалезную платформу ў бок высокай хуткасці сфероідызацыі. Нізкі ўзровень прышчэпкі прымушае платформу рухацца ўніз. На становішча вермікулярнай жалезнай платформы паўплываюць шматлікія фактары, такія як тэмпература перагрэву расплаўленага жалеза, час вытрымкі, хімічны склад сыравіны, тып прышчэпкі і колькасць прышчэпкі.
Самае асноўнае патрабаванне любой тэхналогіі кіравання працэсам - дакладнае вымярэнне і аналіз стану расплаўленага жалеза. Для вермікулярнага жалеза надзейны кантроль вытворчасці патрабуе адначасовага вымярэння крытычнай кропкі актыўнага магнію ад пераходу поўза-попелу, ступені наступнага выгарання магнію і ступені прышчэпкі.
Узор цеплавога аналізу 200 грам атрымліваецца ўстаўкай зонда Xinte ў расплаўленае жалеза пасля сфероідацыі і прышчэпкі. Падчас трохсекунднага ўстаўкі сценка зонда і расплаўленае жалеза дасягаюць стану цеплавой раўнавагі. У адрозненне ад звычайнага шклянкі для ўзору цеплавога аналізу, гэты танкасценны пробоотборник не толькі гарантуе кожны раз аднолькавы аб'ём пробы, але і дазваляе пазбегнуць акіслення ў расплаўленым жалезе, якое выліваецца ў шклянку для пробы. Вымярэнне перагрэву больш дакладнае, таму што ў звычайным цеплавым аналізе няма такой з'явы, як з'ява гвалтоўнай кандэнсацыі.
Як паказана на малюнку 6а, зонд Xinte зроблены з прэсаванай нацягнутай ліставай сталі. У асноўным гэта сферычны кантэйнер. Тонкая сталёвая сценка, якая змяшчае расплаўленае жалеза, мае ізаляцыйны пласт, падобны на вакуумную колбу. Таўшчыня ізаляцыйнага пласта сіметрычна патаўшчаецца ў адпаведнасці з кірункам вышыні, каб забяспечыць раўнамернае рассейванне цяпла і астуджэнне ў навакольным асяроддзі, а вада жалеза zz у ім блізкая да застывання сферычнага цела. У ахоўнай трубцы ў зондзе ёсць дзве тэрмапары N-тыпу. Тэрмаэлемент можна выцягваць пасля кожнага вымярэння і выкарыстоўваць паўторна больш за 100 разоў. Адна з двух тэрмапар размешчана ўнізе кантэйнера, а другая - у цеплавым цэнтры кантэйнера. Паколькі ёмістасць сферычная і свабодна падвешана (гэта адрозніваецца ад звычайнага шклянкі для ўзору цеплавога аналізу, якая ляжыць на кранштэйне для паглынання цяпла), расплаўленае жалеза генеруе раўнамерны цяпло ў кантэйнеры, як паказана на малюнку 6b. Гэты струмень цяпла прымушае бесперапынна абменьвацца расплаўленым жалезам у ёмістасці, утвараючы перагародку патоку на дне зонда.
Каб імітаваць натуральную страту расплаўленага жалеза падчас залівання, на сценцы зонда ёсць пакрыццё, якое ўступае ў рэакцыю з актыўным магніем. Расплаўленае жалеза цячэ па сцяне з пакрыццём, якое рухаецца цеплавым патокам. Пасля рэакцыі ўтрыманне магнію ў расплаўленым жалезе зніжаецца і назапашваецца ў адсеку на дне ёмістасці. Прама кажучы: тэрмапара ў цэнтры зонда вымярае непрарэагавалае расплаўленае жалеза, якое з'яўляецца зыходным станам залівання; тэрмапара ўнізе вымярае стан пасля заканчэння залівання. Рэцэптура рэактыўнага пакрыцця вельмі асаблівая. Трэба дакладна пераканацца, што расплаўленае жалеза, назапашанае ў адсеку, на 0.003% менш актыўна, чым цэнтральнае расплаўленае жалеза. Такім чынам, калі зыходнае ўтрыманне магнію занадта блізка да пункту павароту попелу, расплаўленае жалеза ў адсеку будзе выпрацоўваць шэрае жалеза, якое будзе вымярацца тэрмапарай у гэтай зоне. Такім чынам, у пачатку ліцця майстэрня можа дадаць больш магнію, каб кампенсаваць непазбежныя страты пры спальванні магнію.
Калі тэрмапара ўнізе паказвае вермікулярную жалезную крывую, гэта азначае, што зыходнае ўтрыманне магнію дастаткова высокае, што пасля заканчэння адліўкі не будзе шматкоў графіту.
Малюнак 7-дыяграма эрозіі папярочнага разрэзу зонда Xinte пасля вымярэння пробы. На малюнку вы добра бачыце зону перагародкі, асноўную зону ўзору і трубку абароны тэрмапары. Па меры зніжэння актыўнага магнію на 0.003%у зоне падзелу ўтвараюцца D-вобразная графітавая і ферытавая матрыца. Памер плоскі графітавай вобласці ўнізе непасрэдна адлюстроўвае зыходнае ўтрыманне магнію ў асноўнай плошчы ўзору. Памер гэтай зоны можна вылічыць з выдзеленага ўнізе цяпла. Каэфіцыент рэгрэсіі дысперсіі паміж цеплавыдзяленнем і памерам перагародкі перавышае 0.9, што даказвае, што сувязь паміж імі вельмі блізкая. Вылучаемае цяпло атрымліваецца за час інтэграцыі крывой астуджэння. Гэты метад вымярэння стану расплаўленага жалеза ў току і ў канцы залівання адначасова забяспечвае дакладнасць ўтрымання магнію перад заліваннем.
Паколькі вермікулярнае жалеза вельмі адчувальнае да сфероідызуючых агентаў і прышчэпак, ліцейным заводам немагчыма выкарыстоўваць залішнія метады ачысткі, якія выкарыстоўваюцца ў вытворчасці шэрага і пластычнага жалеза. Як паказана на малюнку 8, з -за сваёй адчувальнасці вермікулярны жалеза стабільны толькі ў квадратным акне, а не толькі ў вобласці магніевай платформы. Надзейны працэс вытворчасці вермікулярнага жалеза павінен кантраляваць сфероідызацыю і прышчэпку ад пачатку да канца, каб гарантаваць, што металаграфічная структура адпавядае задачы.
Якімі б намаганнямі ні прыкладаліся, якім бы строгім ні было кіраванне, ваганні расплаўленага жалеза заўсёды непазбежныя. Не кажучы ўжо пра тое, наколькі дакладныя людзі ведаюць пра апрацоўку расплаўленым жалезам, аднаэтапныя метады апрацоўкі, такія як сэндвіч-метад, не могуць гарантаваць, што кожная апрацоўка патрапіць у вузкае вермікулярнае жалезнае акно. Шматлікія вытворчыя зменныя, такія як каэфіцыент змешвання, тэмпература печы, час вытрымкі, ступень папярэдняга нагрэву коўша з расплаўленага жалеза, хуткасць выстуквання, становішча выстуквання расплаўленага расплаву (унутры або звонку), вага расплаўленага жалеза, стан мяшка сплаву, сфероідызуючы агент фактычнае ўтрыманне магнію (PeSiMg), размяшчэнне сплаваў кожнага пласта ў сэндвіч -метадзе, а таксама пакрыццё піламатэрыялаў і г.д. будуць уплываць на паглынанне магнію. У дадатак да гэтых фактараў, змест актыўнага кіслароду і актыўнай серы таксама зменіць памер і становішча вермікулярнага жалезнага акна. Змены часу знаходжання расплаўленага жалеза ў коўшыку, часу транспарціроўкі і часу залівання зменяць даступны час гарэння.
Аднак самыя непрадказальныя фактары ваганняў - гэта памылкі аператара або адрозненні паміж рознымі аператарамі з -за розных працоўных звычак.
У маштабным масавым вытворчасці адзіным бяспечным спосабам з'яўляецца вымярэнне характарыстык застывання расплаўленага жалеза пасля апрацоўкі. Такім чынам, розныя фактары, якія ўплываюць на памер, становішча і паглынанне сплаву вермікулярнага жалезнага акна, былі ўсебакова вымераны, прааналізаваны і разгледжаны. Затым можна дадаць адпаведную колькасць магнію і прышчэпкі. Кожны чарпак расплаўленага жалеза разліваецца пасля таго, як ён быў прыведзены ў ідэальны стан. Гэты двухступенчаты метад кантролю працэсу вымярэння і рэгулявання зводзіць да мінімуму зменлівасць вытворчасці і цалкам выключае рызыку з'яўлення графіту ў выглядзе ліцця.
Кантроль працэсу вытворчасці вермікулярнага жалеза з коўшам з гарачага металу
Як паказана на малюнку 9, кіраванне працэсам пачынаецца з тэрмічнага аналізу расплаўленага жалеза пасля першапачатковай сферычнай апрацоўкі і прышчэпкі. Згодна з вынікам аналізу, машына для падачы дроту аўтаматычна адлюстроўвае даўжыню дроту, які трэба дадаць з магніем і прышчэпкай, і чакае, пакуль аператар яе запусціць. Калі лінія падачы завершана, коўш неадкладна адпраўляецца на ліццё. Увесь працэс вымярэння і налады займае каля трох хвілін. У гэты перыяд майстэрня можа праводзіць звычайныя працэдуры папярэдняга ліцця, напрыклад выдаленне дзындраў. Гэта забяспечвае бесперапыннасць ліцця ліцця.
З пункту гледжання эксплуатацыі, расплаўленае жалеза не ўтрымлівае магнію, і яго інкубацыйная здольнасць таксама вельмі абмежаваная. Пасля сфероідацыі і прышчэпкі магній і прышчэпкі спачатку з'ядаюць актыўны кісларод і серу ў расплаўленым жалезе, а затым "пераскокваюць" расплаўленае жалеза ў пэўнае становішча на дошцы. У прыкладзе на малюнку 10 індэкс магнію і паказчык прышчэпкі расплаўленага жалеза роўныя 65 і 45 адпаведна. Паколькі асноўныя параметры змены вытворчасці ценю паказаны ў расплаве жалеза пасля вымярэння і апрацоўкі, вынікі тэрмічнага аналізу непасрэдна адлюстроўваюць бягучы стан расплаўленага жалеза. Засталося толькі дадаць адпаведную колькасць магнію і прышчэпкі, каб падняць расплаўленае жалеза з яго бягучага становішча да неабходнай адпраўной кропкі. У прыкладзе на малюнку 10 спачатку дадаюцца сем адзінак магніевых кабеляў, а потым дадаюцца 23 адзінкі кабеляў -прышчэпак. Адпаведнае суадносіны паміж адзінкай індэкса і даўжынёй кабеля адкалібравана ў адпаведнасці з прадуктам і майстэрняй і складзена ў праграме. Зыходзячы з мінулага вопыту амаль 100,000 5 вермікулярных чыгунных адлівак, сярэдняя колькасць дададзенага магніевага кабеля складае 12 метраў на тону. Ён змяшчае 50 грам магнію на метр, а пры разліку пры паглынанні 30%колькасць магнію, дададзенага на тону расплаўленага жалеза, складае ўсяго XNUMX грам. Паколькі сума дабаўкі вельмі малая, а асноўныя змены ўжо адбыліся пры першасным лячэнні, карэкціроўка вельмі эфектыўная і надзейная. Пасля рэгулявання няма неабходнасці праводзіць тэрмічны аналіз.
Пры першаснай апрацоўцы стан пасля апрацоўкі павінен быць ніжэйшым за зыходнае становішча разліву, так што нават калі ўсе фактары, спрыяльныя для паглынання магнію і прышчэпкі, дасягнуць аптымальнага значэння, расплаўленае жалеза дасягне толькі першапачатковага стану разліву . За выключэннем магчымасці залішняй апрацоўкі, расплаўленае жалеза пасля апрацоўкі не знаходзіцца ў стане шэрага і белага жалеза. Для таго, каб зрабіць працэс ліцця больш эфектыўным, індэкс магнію і паказчык прышчэпкі кожнага коўша расплаўленага жалеза адлюстроўваюцца на блок -схеме працэсу. У адпаведнасці са зменлівай тэндэнцыяй блок -схемы, аператар можа рэгуляваць колькасць расплаўленага жалеза, дададзенага ў наступны коўш. Эквівалент вугляроду таксама адлюстроўваецца на экране. Гэтыя дадзеныя былі адрэдагаваны і захаваны ў вытворчым журнале, каб іх можна было прасачыць і вычарпаць, а таксама яны адпавядаюць патрабаванням забеспячэння якасці.
Нягледзячы на тое, што тэрмічны аналіз і наступныя карэкціроўкі могуць забяспечыць вытворчасць вермікулярнага жалеза, рэкамендуецца ўзяць узоры з літровага стакана канчатковага ліцця для аналізу. У параўнанні са звычайнай праверкай якасці, гэты вынік цеплавога аналізу можа забяспечыць онлайн -аналіз і класіфікаваць адлівак, калі гэта неабходна. Мадэляванне страт магнію ў зондзе робіць гэтую "неразбуральную" тэхніку праверкі больш эфектыўнай, чым металаграфічныя і ультрагукавыя метады. Паколькі гэты метад вымярае большы памер выбаркі, ён таксама вызначае, як расплаўленае жалеза застыне ў бліжэйшыя 10-15 хвілін.
Падсумоўваць
Выбар сістэмы кіравання працэсам залежыць ад прадукту і працэсу ліцця. Пры ліцці складаных прадуктаў, такіх як крышка рухавіка з цыліндраў і цыліндр, сістэма павінна адначасова кантраляваць змест магнію і прышчэпкі, каб яна знаходзілася ў вельмі вузкім акне ад пачатку да канца залівання. Каэфіцыент сфероідызацыі павінен складаць ад 0% да 20% (хуткасць паўзучасці ад 80% да 100%) для забеспячэння найлепшага ліцця, механічнай дабаўкі і іншых комплексных характарыстык і найлепшага выкарыстання. Графітавыя плямы шматкоў павінны быць цалкам ліквідаваны, каб прадухіліць мясцовыя дэфекты і слабыя месцы.
Адпраўным пунктам любой сістэмы кіравання працэсам з'яўляецца дакладнае і эфектыўнае вымярэнне стану расплаўленага жалеза. Надзейная буйнамаштабная вытворчасць вермікулярнага жалеза павінна мець даступныя метады кантролю, каб выключыць змены ў працэсе і памылкі працы чалавека. Найбольш эфектыўны спосаб ліквідацыі змяненняў працэсу - правядзенне тэрмічнага аналізу на расплаўленым жалезе пасля сфероідацыі і прышчэпкі. Згодна з вынікамі тэрмічнага аналізу, перад заліваннем дадаткова дадаецца дакладная колькасць магнію і прышчэпкі. Гэты он-лайн метад вымярэння і рэгулявання забяспечвае стабільнасць вытворчасці ліцця і ліквідуе розныя рызыкі, звязаныя з маштабнай вытворчасцю вермікулярнага жалеза.
Калі ласка, захавайце крыніцу і адрас гэтага артыкула для перадруку: Кантроль працэсаў вытворчасці вермікулярнага жалеза
Мінге Кампанія па ліццё пад ціскам прызначаны для вытворчасці і забяспечваюць якасную і высокаэфектыўную ліццёвую дэталь (асартымент ліцейных частак для металу ў асноўным уключае Тонкасценнае ліццё,Кастынг гарачай камеры,Халодная камера ліцця пад ціскам), Круглы сэрвіс (служба ліцця пад ціскам,Апрацоўка з ЧПУ,Выраб цвілі, Апрацоўка паверхні). Любыя замовы для ліцця пад ціскам з алюмінія, ліцця пад магніем або замакам / цынкам і іншыя патрабаванні да адлівак можна звязацца з намі.
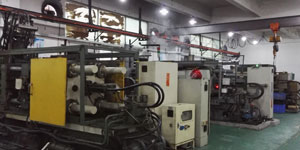
Пад кантролем ISO9001 і TS 16949 усе працэсы ажыццяўляюцца праз сотні сучасных машын для ліцця пад ціскам, 5-восевых машын і іншых установак, пачынаючы ад бластеров і заканчваючы пральнымі машынамі Ultra Sonic. Minghe мае не толькі сучаснае абсталяванне, але і прафесійнае абсталяванне каманда вопытных інжынераў, аператараў і інспектараў, каб спраектаваць дызайн заказчыка.
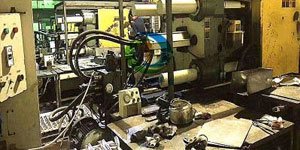
Кантрактны вытворца адлівак з штампаў Магчымасці ўключаюць алюмініевыя часткі для ліцця пад ціскам ад халоднай камеры ад 0.15 фунта. да 6 фунтаў., хуткая налада змены і апрацоўка. Паслугі з дадатковай вартасцю ўключаюць паліроўку, вібрацыю, зняцце задзірын, дробеструйную апрацоўку, афарбоўку, пакрыццё, пакрыццё, зборку і аснастку інструментаў. Матэрыялы, з якімі працавалі, уключаюць такія сплавы, як 360, 380, 383 і 413.
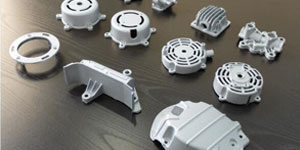
Дапамога ў дызайне ліцця пад ціскам / адначасовыя інжынерныя паслугі. Спецыяльны вытворца прэцызійных адлівак з цынка. Могуць вырабляцца мініяцюрныя адліўкі, адліўкі пад высокім ціскам, адліўкі з некалькіх слайдаў, звычайныя адлівачныя формы, адліўкі пад штампы і незалежныя адліўкі, а таксама адліваныя вырабы з паражніной. Адліўкі могуць вырабляцца з даўжынёй і шырынёй да 24 цаляў у +/- 0.0005 цалі.
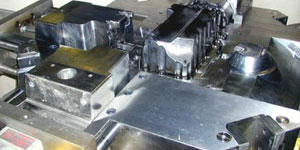
ISO 9001: 2015 сертыфікаваны вытворца адліванага магнію, Магчымасці ўключаюць ліццё пад ціскам магнію пад высокім ціскам да 200 тон гарачай камеры і 3000 тон халоднай камеры, дызайн інструментаў, паліроўка, ліццё, апрацоўка, афарбоўка парашкамі і вадкасцямі, поўны кантроль якасці з магчымасцямі ШМ , зборка, упакоўка і дастаўка.
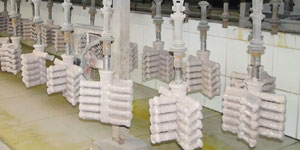
Сертыфікавана ITAF16949 Дадатковая служба кастынгу ўключае ліцця па выплавляемым мадэлям,ліццё пяску,Гравітацыйны ліццё, Кастынг страчанай пены,Цэнтрабежны кастынг,Вакуумнае ліццё,Пастаянная ліццё цвілі, .Можнасці ўключаюць EDI, інжынерную дапамогу, цвёрдае мадэляванне і другасную апрацоўку.
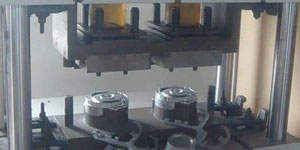
Ліцейныя галіны Тэматычныя даследаванні дэталяў для: Аўтамабіляў, ровараў, самалётаў, музычных інструментаў, плаўсродкаў, аптычных прыбораў, датчыкаў, мадэляў, электронных прылад, карпусоў, гадзін, машын, рухавікоў, мэблі, ювелірных вырабаў, прылад, тэлекамунікацый, асвятлення, медыцынскіх прыбораў, фатаграфічных прылад, Робаты, скульптуры, гукавое абсталяванне, спартыўнае абсталяванне, інструменты, цацкі і многае іншае.
Што мы можам дапамагчы вам зрабіць далей?
∇ Перайдзіце на галоўную старонку для Ліццё пад ціскам Кітай
→Часткі ліцця-Даведайцеся, што мы зрабілі.
→ Параўнаныя парады пра Паслугі ліцця пад ціскам
By Вытворца ліцця пад ціскам Minghe | Катэгорыі: Карысныя артыкулы |матэрыял Ключавыя словы: Алюмініевае ліццё, Цынкавае ліццё, Ліццё магніем, Тытанавы ліццё, Ліццё з нержавеючай сталі, Ліццё з латуні,Бронзавы ліццё,Кастынг відэа,Гісторыя кампаніі,Алюмініевае ліццё пад ціскам | Каментарыі адключаны